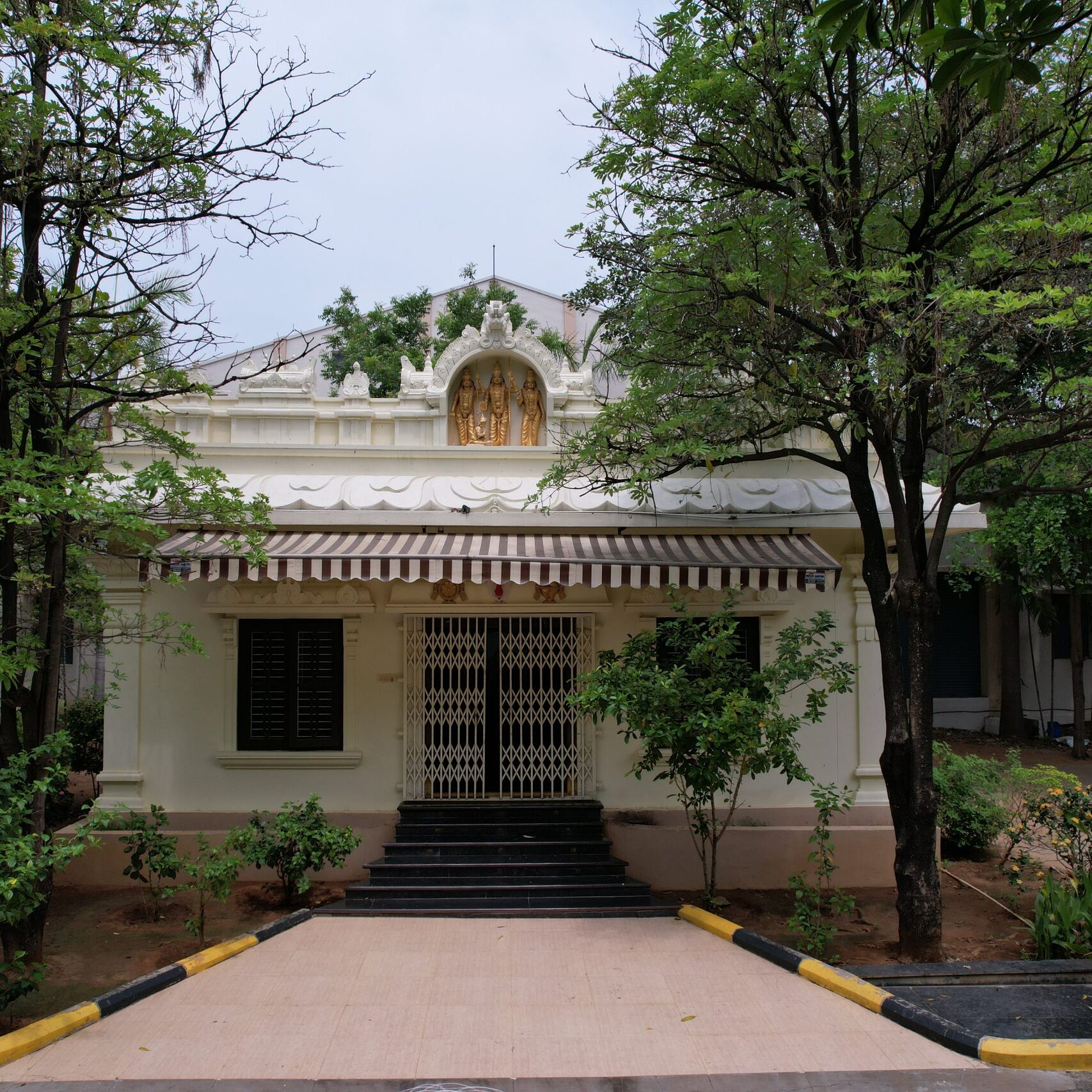
Machinery Maintenance
VIPL has a dedicated team of professionals employed to ensure overall plant maintenance activities. The maintenance team is committed to reaching its maximum production efficiency with the least possible downtime. The team follows preventive maintenance practices as guided by the machine manufacturers. These practices are undertaken at regular intervals, thereby helping to increase the reliability of the equipment and avoiding unexpected breakdowns.
The maintenance team works closely in coordination with the Quality Assurance team to evaluate its critical maintenance activities too. In addition, the maintenance team remains abreast of the new developments in maintenance technology, and its suitable options, to attain optimum production levels.
VIPL is committed to the TPM philosophy, and hence, the maintenance crew is well-versed with MTBR/MTTR as these form the foundation of any maintenance system. The majority of the regular maintenance activities are conducted by the in-house technicians, whereas the critical changes, such as, Carding wire mounting, and compact conversions plus critical activities will be done along with the machine manufacturer’s service team. the Smart Predictive Maintenance (SPDM), such as air leakage measurements, energy consumption, vibration testing, Thermograph analysis are being carried out with the help of external experts periodically.
Machine Optimization & Automation
At VIPL, as a part of machine optimization and automation, the factory is installed with productive machines having the most modern automation at every stage to ensure the highest level of work safety, product quality, and productivity monitoring. In addition, various automated material handling systems are installed. The mill has also installed a fully automatic bobbin transport system from speed frames to ring frames, and auto coners linked to ring frames for fully automatic transportation of bobbins enhancing product quality and productivity, whilst avoiding manual handling. The mill has embraced Total Productive Maintenance (TPM) to minimize machine breakdowns and downtime-led losses. This has resulted in consistent and optimum product quality, achieved by proven intervals of scheduled maintenance and predictive replacement of spares within their lifespan. The ring frames in the units are equipped with individual online individual spindle monitoring systems to improve performance and also reduce manpower.
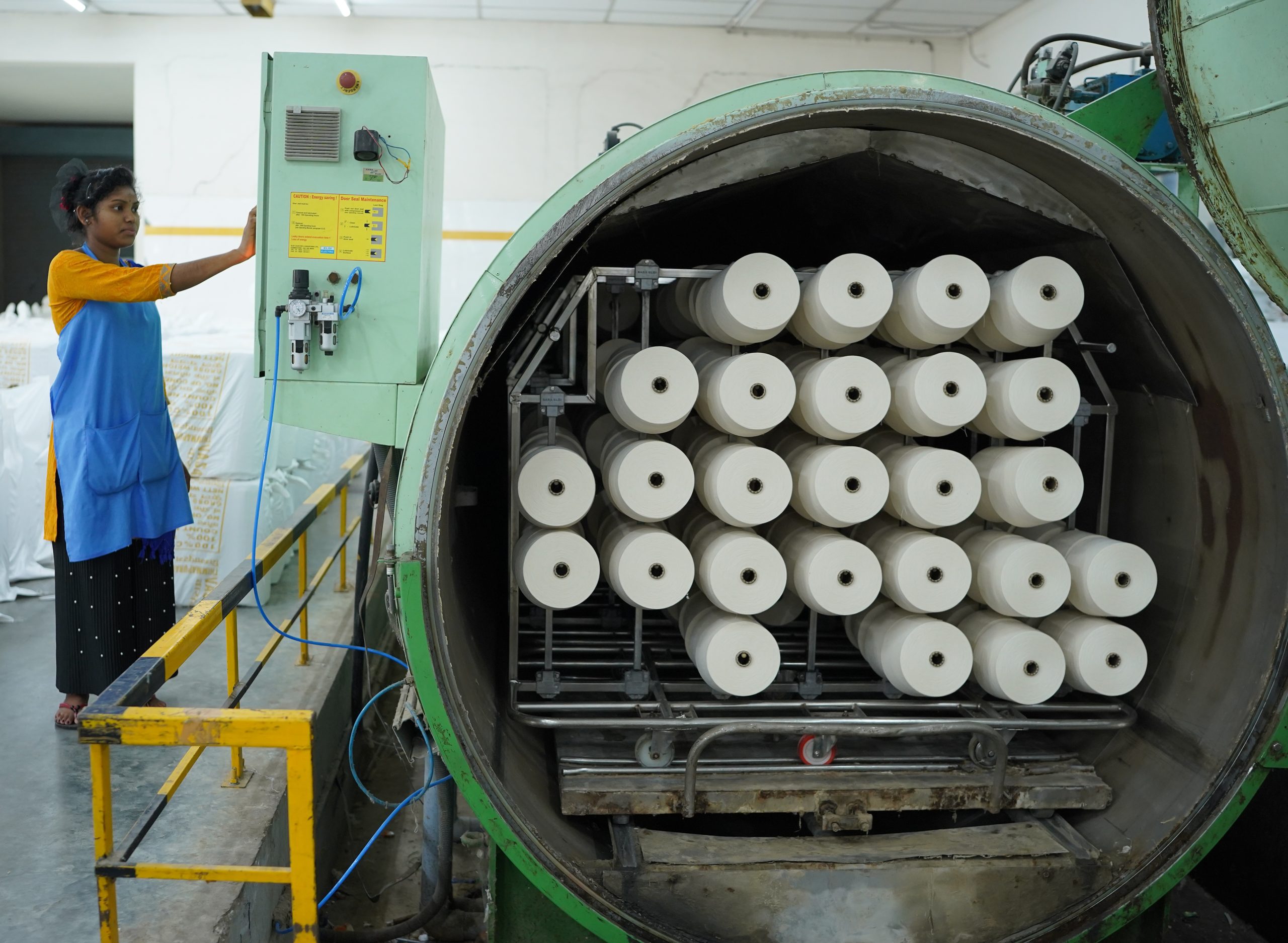